Технология изготовления вывесок
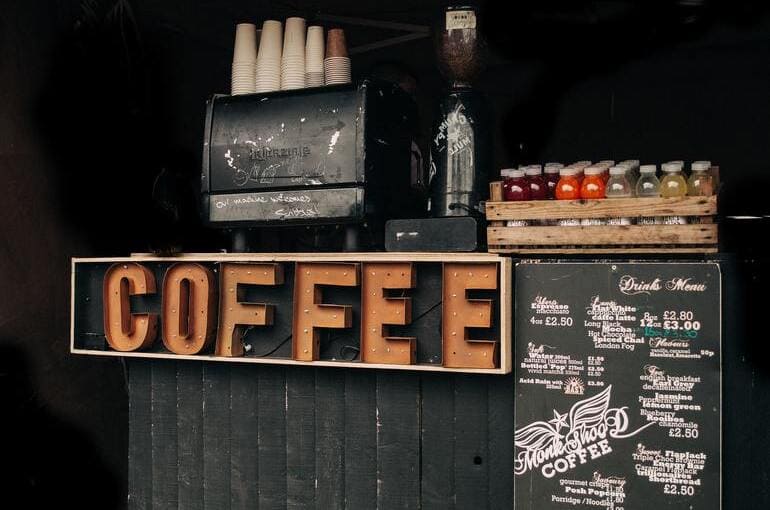
Технология изготовления рекламных вывесок не одна, их несколько, как и самих вывесок. Ну, например, для лайтбокса нужен металлический короб и светодиодный модуль, а для баннерной вывески - нет, а это уже 2 технологии, как минимум. Каждую из них в одной статье мы не опишем, но общие положения их производства постараемся.
Любая технология изготовления вывесок начинается с разработки макета. Его делает заказчик или производитель за отдельную плату. Услугу сегодня легко можно заказать и у сторонней дизайн-студии.
Дизайн на этом этапе рисуют, исходя из корпоративного стиля бренда - как правило, за основу берут фирменные шрифты, визуальные образы и цвета логотипа и других корпоративных знаков.
Формат макета зависит от способа реализации изображения. Если планируется печать, то подойдет как векторный, так и растровый, если нужна порезка - только векторный. Шрифты в любом случае переводятся в вектор, а прозрачности и эффекты растрируются.
Разрешение картинки делают стандартным - 150 dpi. Его можно сократить только, если готовая вывеска не будет просматриваться с расстояния меньше 3х метров (в таком случае качество можно снизить до 90-100 dpi).
Цвета лучше делать в схеме CMYK, НО (!), если заказчик (может, это вы?) - перфекционист, и люфт оттенка приведет его в кому, или, например, необходимо сделать какой-то паттерн на бэкграунде одним и тем же цветом, то цветопроба ОБЯЗАТЕЛЬНА к заказу (+выезд на печать).
Мы прошлись по общим требованиям к макетам вывесок, теперь пройдемся по материалам, с обилием которых растут и технологии наружной рекламы. Раньше вывеску делали в основном из ПВХ, металла и нержавейки с покрытием, сегодня - из чего угодно, и это очень круто для индустрии, ведь можно сколько угодно менять внешний вид вывески и ее технические характеристики, пока не получится тот самый вариант.
Итак, после макета идет подбор материалов и стартует производственный процесс. Станки устанавливаются на лекала и режут, элементы свариваются, комплектующие интегрируются в изделия.
Сегодня основной выбор материалов следующий
ПЛАСТИКИ
- акрил. Его еще называют органическим стеклом, потому что этот пластик прозрачный как обычное стекло. Сейчас это ТОПовый вариант для световых вывесок, хоть и не очень стойкий к физическому и химическому воздействию. Его недостатки перекрывает доступность и простота в работе.
- поликарбонат. Это более дорогой и устойчивый к нагрузкам аналог акрила. Он легко поддается формовке и механической обработке. Хорош и тем, что стандартный размер листа гораздо шире, чем акриловый лист, а это - вывеска бОльшего размера.
- вспененный ПВХ. Дешевый, но весьма рабочий в условиях постоянного УФ-излучения и других неблагоприятных погодных условиях. Стойкий также к химии и солям. Легкий, но жесткий, подходит для печати.
- полипропилен. Пузырьковый или сотовый. Такой же дешевый и стойкий к температуре, влаге и солнечным лучам материал. Отлично держит краску и пленки без выцветания. Наиболее доступное решение для аппликации пленкой или печати (цифровой планшетной или трафаретной).
- полистирол. Чаще всего используется для вывесок внутри помещений, но при интеграции специальной УФ-защиты (под заказ) может успешно работать в наружных конструкциях до ~5 лет.
КОМПОЗИТЫ
- дибонд. Дорогой высокопрочный материал из пластин алюминия толщиной 0,3 мм каждая с прослойкой полиэстера. Необработанным выглядит как зеркальная панель и смотрится очень эффектно. Отлично подходит для резки, фрезеровки, сгибания, сверления, поддается ламинированию.
- алюкобонд. Аналогичный материал, но с пластинами толщиной 0,5 мм.
- плабонд. Также алюмкомпозит, но с пластинами толщиной 0,3 мм или 0,21 мм.
Несмотря на то, что композиты не обладают светопропускной способностью, их активно используют в производстве лицевых панелей в световых вывесках. Для этого в них вырезают буквы (или другие фигуры) и ставят акриловую подложку, проектирующую через них свет с задней панели. Подробно прочитать об этом можно в статье Что такое лайтбокс.
ПЛАСТИКОВЫЕ ТКАНИ
- баннерная ткань. Ламинированное или литое ПВХ-полотно, армированное нитью полиэстера, которое отлично работает в широкоформатной печати.
- текстиль. Полиэстеровое полотно, которое подходит для печати любыми типами чернил (УФ, латексными, сублимационными) и максимально просто ведет себя в производственном процессе. Его транспортировка и монтаж также гораздо проще, чем с другими печатными носителями.
Материалы перечисленных групп используются в первую очередь для изготовления лицевых панелей вывески. Все они, кроме композитных, имеют высокую светопропускаемость.
МЕТАЛЛЫ
- алюминий. Любимчик производителей - легкий, прочный, неприхотливый в обработке нержавеющий материал с относительной доступностью.
- оцинкованная сталь. Дешевый аналог алюминия, но недолговечный, потому что может ржаветь.
- профильная труба. Самый дорогой металлический вариант, но крепкий и идеальный для массивных конструкций. Для спасения от коррозии покрывается краской.
Материалы этой группы наряду с твердым ПВХ используются в следующем этапе производства - изготовление силового каркаса, профиля конструкции. Перед сборкой каркаса его элементы могут подлежать оклейке или окраске, если есть требование к их цветовому решению.
При изготовлении световых вывесок внутри каркаса монтируют элементы подсветки (проволочные сети, лампочки, дроссели, пускорегулирующие аппараты и т.д.). В качестве источника света внедряют светодиодный, люминесцентный или неоновый блок.
Дальше идет этап нанесения изображения. Здесь, как вы уже поняли, два основных варианта - печать и порезка. Печатают на некоторых полимерных и композитных материалах, баннерной ткани, текстиле или пленке, вырезают из самоклейки, прозванной в народе “оракалом” (хотя Оракал - это всего лишь производитель).
САМОКЛЕЮЩИЕСЯ ПЛЕНКИ
- для печати - офсетной или цифровой. Их немыслимое множество - матовые, глянцевые, перфорированные, прозрачные.
- для плоттерной порезки - такие также представлены в изобилии цветов и форматов, идеальны для нанесения изображений путем аппликации.
После сборки вывеска подлежит многократному тестированию на производстве и дальнейшему монтажу.